Modified Technique for Making Auto-polymerized Polymethylmethacrylate Resin Custom Tray
Ahila Singaravel Chidambaranathan1, Ramesh Reddy2, Suresh Rajendran3, Muthu Kumar Balasubramaniam4
1 Reader, Department of Prosthodontics, SRM Dental College, Chennai, Tamil Nadu, India.
2 Reader, Department of Prosthodontics, SRM Dental College, Chennai, Tamil Nadu, India.
3 Senior Lecturer, Department of Prosthodontics, SRM Dental College, Chennai, Tamil Nadu, India.
4 Professor and Head, Department of Prosthodontics, SRM Dental College, Chennai, Tamil Nadu, India.
NAME, ADDRESS, E-MAIL ID OF THE CORRESPONDING AUTHOR: Dr. Ahila Singaravel Chidambaranathan, Reader, Department of Prosthodontics, SRM Dental College, Bharathi Chalai, Ramapuram, Chennai-89, Tamil Nadu, India.
E-mail: ahilasc@yahoo.co.in
Custom made tray for dental impression is designed to provide a uniform space for the impression material and thereby improve the accuracy of the resultant working cast. Auto-polymerized acrylic resins have been the most commonly used material for the fabrication of these trays. The custom tray produces more accurate and reliable results for inter-abutment distance at the occlusal and gingival level than stock trays. This article describes a modified technique for fabrication of auto-polymerized Polymethylmethacrylate (PMMA) resin trays.
The clinical success of the indirect restoration in prosthetic dentistry requires an accurate working cast which depends upon the accuracy of the final impression [1]. An accurate registration of oral structures requires uniform thickness of impression material and rigid and accurate custom tray to support the material [2].
Custom trays are made up of auto-polymerizing Polymethyl-methacrylate (PMMA) resin, thermoplastic material and visible-light curing resin. The tray materials are supposed to be rigid, dimensionally stable, retentive to impression materials or adhesive and moisture resistant. They should be easy to fabricate, economical and have long shelf life. Trays made from shellac or through vacuum forming procedures have low modulus of elasticity, while those made of composite resin materials have insufficient constancy of shape and volume [3].
The introduction of auto-polymerized PMMA polymers brought significant improvement to the mechanical properties of custom trays. Furthermore, the relatively complicated fabrication techniques require more time in the dental laboratory. This article described a modified laboratory technique for making autopolymerized acrylic resin tray.
Technique
The primary cast was prepared and the outline of the vestibule was marked with blue color, tray border with indelible pencil and the spacer extension with red color pencil [Table/Fig-1]. The undercuts were analyzed with the help of a surveyor and blocked out with wax. The relief areas in maxilla and mandible were marked and relieved with base plate wax (Modeling wax, The Hindustan Dental Products, Hyderabad, India), approximately 1-1.5mm thick and the spacer wax was adapted throughout the extent of special tray (2mm short) coinciding with the second line, except the posterior palatal seal area in maxilla and buccal shelf area in mandible. Wax (2x4mm) in the canine and molar area was removed for tissue stop [Table/Fig-2].
Diagnostic casts with reference line.
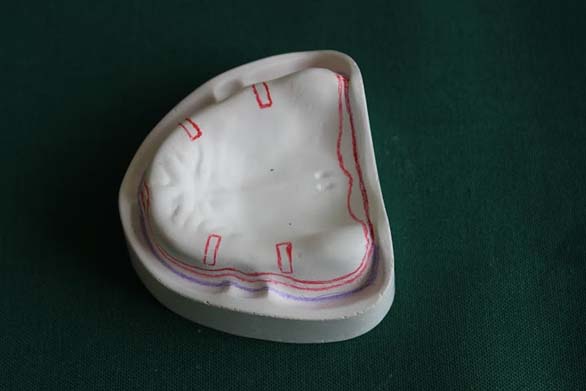
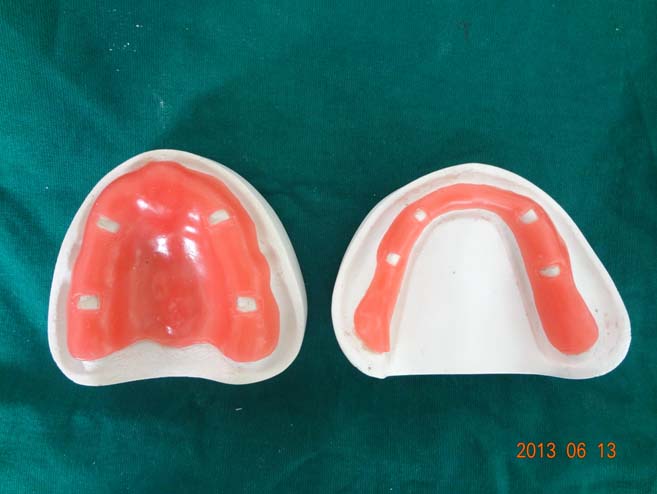
Block out of the cast up to the tray border reference line was done with poly vinylsiloxane (Photosil, DPI, Mumbai, India) putty impression material [Table/Fig-3,4]. The cast was painted with separating media (Cold Mold Seal, DPI, Mumbai, India) and allowed to dry. The flange of the tray was made with autopolymerized PMMA resin (RR Cold Cure, DPI, Mumbai, India) using the sprinkle-on technique. The tray was 2 to 3mm in thickness and the handle was about 3-4mm thick, 8mm wide and of 8mm height, made to extend vertically from the crest of the anterior ridge and a right angle bend was made so that the handle extended forward to about 10-15mm. For the mandibular special tray, the handle was of 20mm height from the sulcus which ran vertically and parallel to lips and two additional handles made over first molar crestal region approximately of 8mm height, 3-4mm thickness and 8mm width. The tray borders were smoothed with grid paper [Table/Fig-5].
Blocking out of tray border with dental plaster and impression compound.
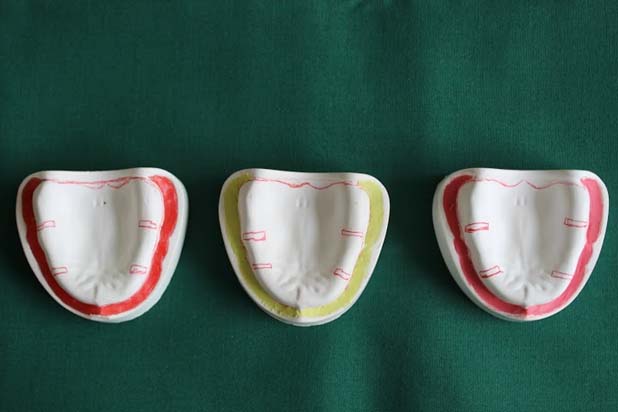
Blocking out of tray border with wax, clay and polyvinyl siloxane.
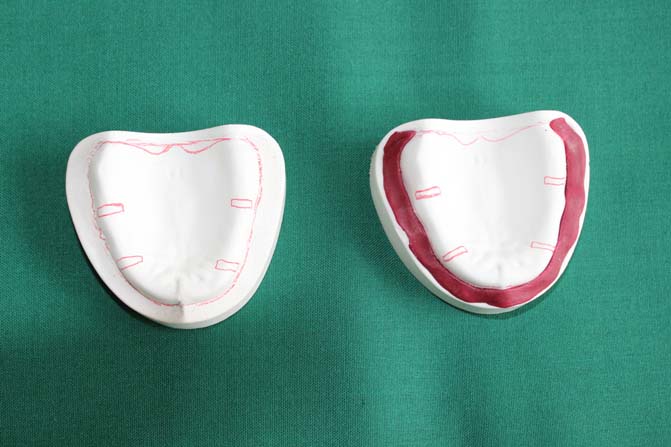
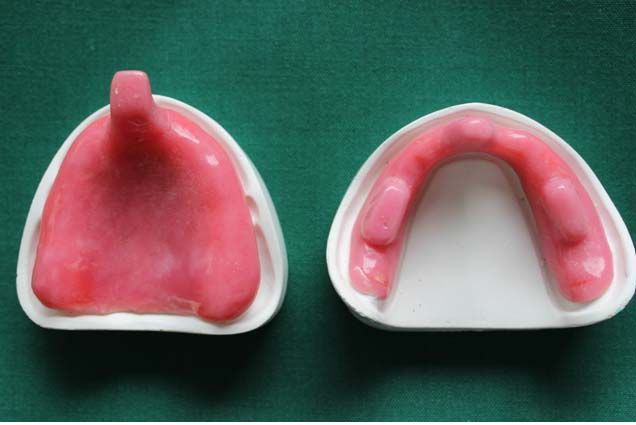
Discussion
Stock trays may provide acceptable clinical results when used for small restorations but inaccuracies in the impression may be magnified in larger restorations [4,5]. The use of a custom tray is indispensable for the fabrication of precise working casts [6,7]. The latter may necessitate adjustments, an increase in chair side time, a need for a new impression, patient discomfort, increased cost and stress and frustration for the dentist.
There are distinct clinical advantages associated with design and use of the custom tray when compared to the stock tray. Custom tray provides homogeneous thickness of impression material all through the tray whereas the use of stock trays can cause discrepancy in thickness of the material leading to dimensional changes and inaccuracies in the working cast [7–9]. The borders of the custom tray can be determined by two methods. Either the periphery is outlined with a disposable indelible marker on the impression (the preferred option) or the outline is somewhat arbitrarily marked on the poured cast in the laboratory [10].
The light cured tray produced resultant casts that were less consistent than those of autopolymerized types, and this difference in behaviour may be caused by their greater liability in the hands of the operators [11]. This liability may lead to an uneven thickness of tray material throughout the tray, especially at the margin. Light curing resins have lower viscosity than the other materials and also have tacky feel during manipulation, both factors leading to a thinner, poorly adapted tray margin that may not resist the forces applied to it during and after impression making [12].
In this technique rigid materials like impression compound and dental plaster were used to block out the space between the vestibule and the border of the tray. Dental plaster bound with the diagnostic cast. So that post-treatment evaluation of the cast was difficult if the dental plaster block out method is followed. Impression compound is a good material for block out, while retrieving the tray impression compound stuck to the borders.
Clay is an easily moldable and adaptable material but it bound to the periphery of the resin tray. Hence, the tray should be disinfected chemically. It may react with the underlying wax spacer. Wax also can be used for blocking out material but the wax was melted and had been spreaded along the surface of the cast. For post-operative evaluation, sometimes the cast may be damaged.
Polyvinyl siloxane is the material of choice for blocking out the space up to the tray border. It is a moldable, adaptable and easily removable material with adequate working time. It won’t react with PMMA resin but it is expensive. We can evaluate the diagnostic cast after the treatment. The advantage of this technique is minimal finishing time in the laboratory. It needs minimal chair side time for correcting the extension of the border clinically.
Conclusion
This article described a modified technique for making custom tray which will reduce the laboratory and chair side time. Fabricating an indirect custom impression tray requires planning, good diagnostic cast and minimum laboratory time. The custom tray conserves the volume of material required for the impression; thus, cutting the cost incurred, as the material used for each impression is reduced. Also, a streamlined design would be comfortable for the patient while making the impression.
[1]. Terry DA, Leinfelder KF, Geller W, Aesthetic & Restorative Dentistry: Material Selection & Technique 2009 Stillwater, MinnEverest Publishing Media [Google Scholar]
[2]. Payne JA, Pereira BP, Bond strength of three nonaqueous elastomeric impression materials to a light-activated resin tray Int J Prosthodont 1992 5:55-58. [Google Scholar]
[3]. Hyun-Kyung Kim, Ik-Tae Chang, Seong-Joo Heo, Jai-Young Koak J, The effects of custom tray material on the accuracy of master cast reproduction Korean Acad Prosthodont 2001 39:282-96. [Google Scholar]
[4]. Stackhouse JA, Dimensional change of custom acrylic impression trays J N J Dent Assoc 1976 47:28-29. [Google Scholar]
[5]. Boulton JL, Gage JP, Vincent PF, Basford KE, A laboratorary study of dimensional change for three elastomeric impression materials using custom and stock trays Aust Dent J 1996 41:398-404. [Google Scholar]
[6]. Johnson GH, Craig RG, Accuracy of addition silicones as a function of technique J Prosthet Dent 1986 55:197-203. [Google Scholar]
[7]. Eames WB, Sieweke JC, Wallace SW, Rogers LB, Elastomeric impression materials: Effect of bulk on accuracy J Prosthet Dent 1979 41:304-07. [Google Scholar]
[8]. Gordon GE, Johnson GH, Drennon DG, The effect of tray selection on the accuracy of elastomeric impression materials J Prosthet Dent 1990 63:12-15. [Google Scholar]
[9]. Thongthammachat S, Moore BK, Barco MT 2nd, Hovijitra S, Brown DT, Andres CJ, Dimensional accuracy of dental casts: Influence of tray material, impression material, and time J Prosthodont 2002 11:98-108. [Google Scholar]
[10]. Zarb Bolender, Prosthodontic treatment for edentulous patients 12th editionElsevier Publication:223-25. [Google Scholar]
[11]. Shafa Zaree Z, Mosharraf R, The effects of custom tray material on the accuracy of master casts J Contemp Dent Pract 2008 9:49-56. [Google Scholar]
[12]. Luis J, Martinez J.A, von Fraunhofer, The effect of custom tray material on the accuracy of master casts J Prosthod 1998 7:106-10. [Google Scholar]