Background
Nowadays, organizations try to improve their services and consequently adopt management systems and standards which have become key parts in various industries. One of these management systems which have been noticed in the recent years is Integrated Management System that is the combination of quality, health, safety and environment management systems.
Aim
This study was conducted with the aim of evaluating the improvement trend after establishment of integrated management system for health, safety and environment indicators, in a pharmaceutical industry in Iran.
Materials and Methods
First, during several inspections in different parts of the industry, indicators that should have been noted were listed and then these indicators were organized in 3 domains of health, safety and environment in the form of a questionnaire that followed Likert method of scaling. Also, the weight of each index was resulted from averaging out of 30 managers and the viewpoints of the related experts in the field. Moreover, by checking the documents and evidence of different years (5 contemplation years of this study), the score of each indicator was determined by multiplying the weight and score of the indices and were finally analysed.
Results
Over 5 years, scores of health scope indicators, increased from 161.99 to 202.23. Score in the first year after applying the integrated management system establishment was 172.37 in safety part and in the final year increased to 197.57. The changes of environmental scope rates, from the beginning of the program up to the last year increased from 49.24 to 64.27.
Conclusion
Integrated management systems help organizations to improve programs to achieve their objectives. Although in this study all trends of health, safety and environmental indicator changes were positive, but at the same time showed to be slow. So, one can suggest that the result of an annual evaluation should be applied in planning future activities for the years ahead.
Introduction
Nowadays, competitive and global markets require providing higher quality services to their customers. In this area, for organizations to increase their chance of success, have no choice but to make effort to manage their business, improve their level, and to be compatible with global standards [1,2].
The factors such as organizational safety policy, training, inspection, incentives and penalties and workers attitude must be considered for improving safety performance [3]. Management systems and standards have become a key part of an organization’s lifeline and a prerequisite for survival in the 21st century [4]. The goal of continual improvement toward achieving and sustaining decent, safe and healthy working conditions and environment is promoted in the 2003 International Labour Organization Global Strategy on Occupational Safety and Health [5].
One can generalize performance improvement to different aspects, such as quality, safety, health and environment in a company, therefore, this element is a part of a company business and consequently a country’s business. In addition, this element has been emphasized in national regulations of most countries and also international laws.
These days, 3 credible management systems which are applied in many companies are Quality Management System, Environment Management System and Occupational Health and Safety Assessment Series [6].
To improve the organization’s production and services, each of these systems cover special scopes, such as quality, environment, industrial safety and occupational health, thus, one of the main purposes of these systems establishment is ensuring these issues in being considered in company strategies.
Due to specific requirements to establish management systems separately, this not only culminate in complexity and confusion, but will also create problems such as, waste of time, great deal of documents, reduction in efficiency and contrast between policies and objectives [7,8]. So in order to prevent these difficulties, management systems were merged in a single system, titled Integrated Management System (IMS). The contemplation behind the concept of IMS is that, tasks should be done through an integrated system instead of several single systems. The role of performance evaluation is checking, reviewing, judging and determining weaknesses and strengths and over a scientific process, converting weaknesses into strengths [9].
In performance evaluation, both aspects of work process and outcomes can be considered, so performance evaluation approach is based on both diagnosis and prevention of risks.
Overall performance of an organization is reported with negative events, such as, injuries and occupational diseases whilst performance includes positive measures [10].
Performance Indicators Can Be Classified as Follow
a) Quantitative indicators
Indicators which are numerical, for instance, the number of conducted audits, injury rates, number of deaths or number of lost days [11].
b) Qualitative indicators
Indicators that describe overall condition or behavior of organization, for example management commitment rating to improve safety and health programs from the employees’ viewpoint [11,12].
Aim
The aim of this research was continuous trend evaluation of health, safety and environmental indicators for 5 years (2008-2012) after establishment of IMS in a pharmaceutical industry in Iran.
Materials and Methods
In order to investigate the changes happening in the trend of health, safety and environment indicators, determining the main activities and also defining the level of importance in each activity was important. Therefore, at first, during several inspections of different parts of the industry, important indicators were listed by researchers and then were organized in 3 domains of health, safety and environment in the form of a questionnaire which followed the Likert’s method of scaling based on relative importance (in which 1 indicates very poor to 5 indicates too much). For questionnaire validation, the questionnaire was sent to 5 faculty members and 5 Health, Safety & Environment specialists and their opinions were mentioned for questionnaire revision.
Finally, for the evaluation of health, safety and environment indicators, 31, 20 and 12 indices such as medical examination of employees, risk assessment program and energy consumption management were specified respectively. The weight of each index was obtained from averaging out of 30 managers and related experts viewpoint. For ethical purposes, and to maintain confidentiality, the questionnaires were distributed and filled anonymously. Also, blind data checking was applied.
The questionnaires were completed with the help of managers, production supervisors, Health, Safety & Environment and quality control personnel. Then the weight of each indicator was determined with the point allocation method. Moreover, to assess the internal consistency of the questionnaire in present study, the reliability of examiners was mentioned by determining the Cronbach’s Alpha that was 0.76.
At the next step, all the available documents and statistics over considered years (2008-2012) in the study were listed and evaluated. Then, based on Likert’s scaling criteria for each index at different years, a point between 0-4 was allocated. (no action conducted=0, poor=1, moderate= 2, acceptable=3, perfect=4).
Statistical Analysis
The final score of each index for every year was calculated by multiplying the weight and score of each index. The SPSS software was used for data analysis.
Results
Based on results of the present study ([Table/Fig-1]) the total points of health scope indicators enhanced from 161.99 to 202.23. In field of safety, calculated point in the first year of establishment of the integrated management system was 172.37, but at the last year increased to 197.57. Alterations of environment field points from first year up to the last year increased from 49.24 to 64.27.
Results of health, safety and environmental indicators scores
Field of Indicators | 1st year | 2nd year | 3rd year | 4th year | 5th year |
---|
Health | 161.99 | 182.81 | 181.11 | 188.07 | 202.23 |
Safety | 172.37 | 172.37 | 179.7 | 186.75 | 197.57 |
Environment | 49.24 | 49.24 | 52.84 | 63.7 | 64.27 |
Total | 383.6 | 407.42 | 413.65 | 438.52 | 464.07 |
As can be seen in [Table/Fig-2], in the best situation, countable scores for health, safety and environmental fields were 432.88, 298.64 and 169.68 respectively, and the total point of HSE-MS were 901.2. [Table/Fig-3] shows the Score Ratio to optimal situation for all the research years.
Optimal conditions of health, safety & environment scores in this industry
Field | Number ofindicators | Average of relativeimportance | Coefficient of theactions condition(perfect) | Optimalconditionscores |
---|
Health | 31 | 3.491 | 4 | 432.88 |
Safety | 20 | 3.733 | 4 | 298.64 |
Environment | 12 | 3.535 | 4 | 169.68 |
Total | --- | --- | --- | 901.2 |
Comparison of proportion of health, safety and environmental indicators scores
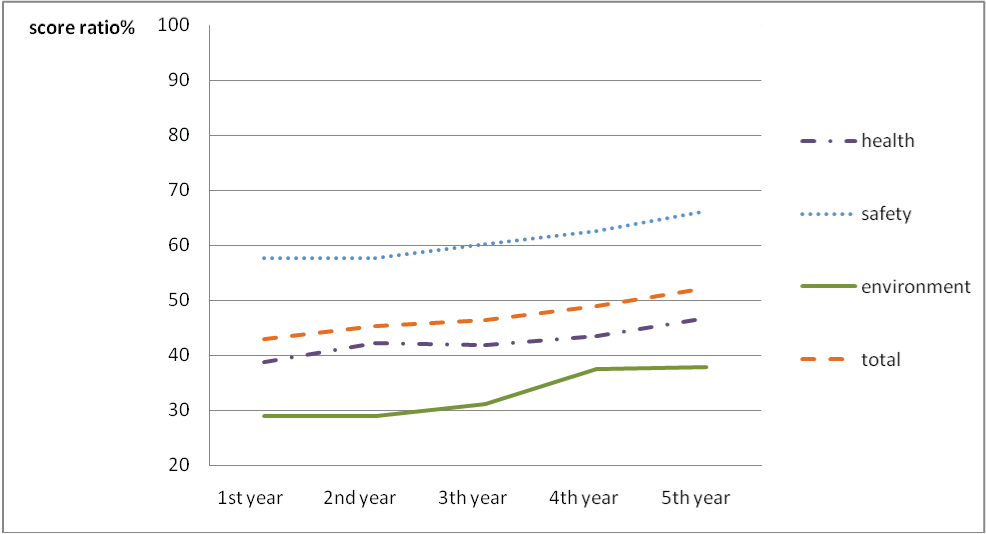
Discussion
Today, the long-term health of any organization depends on their commitment to continuous improvement. One of the main interests in occupational safety and health management system is the capacity of measuring the performance of the system and also it’s improvement over time [5,13]. For this purpose responding to customer needs and other requirements imposed by both regulators and the market place, organizations now find themselves having to confirm to a building number of management standards [14]. Performance indicators are internal criteria that organizations used to view, understand and predict the imagination and interference of employees, customers, contractors and society and improving its performance in respect [15].
The implementation and certification of quality, environmental and occupational health and safety management systems have become a priority for many organizations. They are viewed as a symbol for success and a prerequisite for survival [16].
In continuous improvement studies by IMS, the role of integrated management has been identified as an effective indicator in organization performance improvement and increasing employees’ participation. Moreover, improvement of organization performance has been emphasized as a remarkable outcome of the IMS. Implementation of several management systems such as health and safety programs in form of IMS have some advantages such as reducing documentation, customer increasing satisfaction, better communication, fewer accidents, less delay in tasks and services through, checking related hazards to work places, decreasing the likelihood of occupational diseases, providing higher levels of work conditions, reducing costs related to accidents and motivating employees [17,18]. The standard requires a health and safety policy planning procedures for the identification of hazards and risks, and control measures concerning accidents connected to health and safety [19]. Management systems apply continuous improvement tools such as corrective actions and preventive activities in order to achieve company goals. Labour training related indicators or management of potential hazards has been emphasized as a part of positive performance indicators [20]. It is worthwhile to mention that indicators help us to predict future events and consequently to show suitable reactions [9].
To achieve the objectives of this study, standard indicators for assessment of HSE factors were identified. Then, data was collected for all indicators for 5 years. In the study conducted by Mohammad fam and colleagues, balanced score cards were introduced as a proper tool for assessment of organization performance [21].
The results showed that more focus has been on the safety programs in this industry and less attention has been paid to environmental programs. However, the trend of improving environmental conditions has been better than health and safety.
On the basis of countable score for health, safety and environment scopes of this industry, in the last year of the study, earned scores in health, safety and environment fields were 46.7%, 66.2% and 37.8% of optimal condition scores and total countable score of HSE indicators in this study at the last year was 464.07 based on optimal condition scores (901.2). As pointed out, safety program score has been better off than health and environmental and this shows that more attention is paid to safety in this industry. Gained scores for HSE indicators was 51.5% of optimal condition that indicates an average situation.
In order to improve the HSE climate and to establish the HSE culture in this industry, effective actions should be considered. Jaafari and colleagues have mentioned that after safety training in their study, the total value of safety climate scores increased [22]. For purpose successful in this area, it is necessary to engage the top management, the program acceptance of all employees and to overcome resistance to changes [23]. As well as periodic evaluation, the design and implementation of a system of reward and punishment towards improved behaviors and implementation and operation of comprehensive system of self-reporting can be suggested [24].
Limitation
The main limitation of the study was that considerable time and effort was put into checking several archives for documents and non-homogenous data.
Conclusion
Integrated management systems help organizations to improve programs to achieve their objectives. Although in this study all trends of health, safety and environmental indicator changes were positive, but at the same time showed to be slow. Thus, one can recommend that the result of annual evaluations should be mentioned in planning of programs and activities for future years. For this purpose, leadership commitment has an important role, and also workers’ communication, better documentation of activities and more attention to training of personnel should be considered.
[1]. Little AD. HSE auditing: Fundamentals, skills and techniques for team members. NPC Course Manual. 2005 [Google Scholar]
[2]. Davis ML, Cornwell DA, Introduction to environmental engineering 1998 3rd edMcGraw-Hill Inc [Google Scholar]
[3]. Prasad SVSR, Rao YP, Chalapathi PV, Prioritizing the elements of OHSAS-18001 in construction segments in India, AHP approach International Journal of Occupational Health 2013 5(4):159-65. [Google Scholar]
[4]. Azadeh MA, Creating highly reliable manufacturing system: An integrated approach International Journal of Reliability, Quality and Safety Engineering 2000 7(3):205-22. [Google Scholar]
[5]. ILO. International Labour Organization. OSH management system: A tool for continual improvement. 2011 [Google Scholar]
[6]. Veltri A, Safety, health and environment strategies available to firms and being firms: A conceptual framework for formulating strategy The Journal of SH&E Research 2008 5(3):1-27. [Google Scholar]
[7]. International Association of Oil & Gas Producers. Health performance Indicators. OGP report. 2000 [Google Scholar]
[8]. International Association of Oil & Gas Producers. Health performance Indicators. A guide for the oil and gas industry; 2007 [Google Scholar]
[9]. Jackson SL, The ISO 14001 implementation guide: Creating an integrated management system 1997 John Wiley and Sons Inc [Google Scholar]
[10]. Mirsaeidifarahani SH, Chitsaz Gh, Continual improvement with integrated management system International Scholarly and Scientific Research & Innovation 2010 4(6):1082-86. [Google Scholar]
[11]. Roberge CL, It’s all about attitude Industrial Distribution 1999 88(5):122-27. [Google Scholar]
[12]. UK Oil and Gas industry trade associations. Step change in safetyleading performance indicators, guidance for effective use. 2006; www.oil-gas-safety.org.uk [Google Scholar]
[13]. Kovach JV, Cudney EA, Elrod CC, The use of continuous improvement techniques: A survey based study of current practices International Journal of Engineering, Science and Technology 2011 3(7):89-100. [Google Scholar]
[14]. Pojasek RB, Is your integrated management system really integrated? Environmental Quality management 2006 16(2):89-97. [Google Scholar]
[15]. Mohammadfam I, NaslSaraji G, Kianfar A, Mahmoudi Sh, Developing the health, safety and environment excellence instrument Iranian Journal of Environmental Health Science & Engineering 2013 10(7):1-5. [Google Scholar]
[16]. Zeng SX, Janothan J, Shi GX, A synergic model for implementing an integrated management system: An empirical study in china Journal of Cleaner Production 2007 15(18):1760-67. [Google Scholar]
[17]. Sustainability Reporting. Using environmental, health & safety, social and economic performance Indicators 2005 [Google Scholar]
[18]. Khanna H, Laroyia SC, Sharma DD, A Survey on Indian experience on integrated management standards (IMS) International Journal for Quality Research 2009 3(3):1-5. [Google Scholar]
[19]. Granerud L, Rocha RS, Organizational learning and continuous improvement on health and safety in certified manufacturers Safety Sciences 2011 49:1030-39. [Google Scholar]
[20]. Simpson I, An investigation into the use of positive performance indicators to measure OHS performance 2006 School of Safety Science University of New South Wales [Google Scholar]
[21]. Mohammadfam I, Azadeh A, Jafari M, Kianfar A, The introduction of a fuzzy expert system based on balancedscorecard for measuring the effect of Health, Safety and environment management system on organizations Sha J Sci Tech 2008 53:137-45. [Google Scholar]
[22]. Jafari MJ, Gharari M, Ghafari M, Omidi L, Kalantari S, Asadolahfardi GR, The influence of safety training on safety climate factorsin a construction site International Journal of Occupational Health 2014 6(2):1-7. [Google Scholar]
[23]. Landwojtowicz AK. Determinants of the concept of continuous improvement in manufacturing company, case study. 9th Research/Expert Conference with International Participations “Quality 2015” June 10-13, 2015 [Google Scholar]
[24]. Mohammadfam I, Nikoomaram H, Fardian M, Evaluation of health, safety and environment (HSE) culture International Journal of Occupational Health 2013 5(1):1-5. [Google Scholar]