The use of resilient lining materials is useful in removable prosthodontics, because of their capability of restoring health to inflamed mucosa, leading to equal distribution of functional load on the denture surface and retention of the prosthesis [1–4].
Proper finishing and polishing of dental materials are important aspects of clinical restorative procedure [5,6]. Finishing refers to the gross contouring or reduction of the restoration to obtain the desired anatomy. Polishing refers to the reduction of the roughness and scratches created by the finishing instruments [4,6]. In the oral cavity, most bacteria can only survive if they adhere to the hard surfaces. Different hard surfaces are available in the oral cavity (teeth, filling materials, dental implants, or prosthesis), all with different surface characteristics [7,8]. Rough surfaces (crowns, implant abutments, and denture bases) accumulate and retain more plaque than smooth surfaces [8,9].
Rough surfaces may cause severe complications like inflammation of the mucosa, sore spots [4] chronic irritation leads to ulcers, and colonization of micro-organisms [6–10]. This is especially true for the buccal flange of the denture base, where the liner material interfaces with the hard base and both are exposed to the oral environment, and fitting surface of the denture base [4]. Although smoother surfaces have been shown to be achievable by polishing, but the polishing of the fit surface may significantly affect adjacent non machined areas unless a very precise polishing technique is adopted [10]. Microbial colonization is an essential first step in the development of infection [11]. The fitting surface of the denture can act as a reservoir of Candida albicans in denture stomatitis [11].
Machining long term resilient liner materials generally is difficult because they tend to pull when adjusted with burs. Moreover, liner materials have a lower glass transition temperature than hard acrylic resin; if liners are subjected to too much pressure, generated heat may soften and distort the material [4]. Therefore, it is important to know the surfaces of different denture base materials after machining by instruments in routine clinical use and to identify a satisfactory method of leaving as smooth a surface as possible.
In the present study an effort has been undertaken to evaluate the surface roughness of heat cure acrylic denture base resin and two soft-liners after being subjected to machining with tungsten carbide bur and stone bur. The aim of the study was to evaluate the effects of surface machining by tungsten carbide bur and stone bur on conventional denture base resin (Lucitone 199) and two soft liners (GC supersoft and Permasoft) using Scanning Electron Microscopy. The objectives were: 1) To compare the surface roughness produced by tungsten carbide bur and stone bur on conventional heat cure denture base resin (Lucitone 199), with that on GC supersoft and Permasoft softliner. 2) To identify the satisfactory method of leaving as smooth a surface as possible. 3) To suggest measures for clinical application.
Materials and Methods
The study was carried out in the Department of Prosthodontics, Kamineni inistitute of dental sciences, Narketpally, Nalgonda, Telangana state and SEM evaluation in IICT, Hyderabad. Thirty 15×15×1.5mm square shaped acrylic resin specimens were fabricated with each of three acrylic resins: Lucitone 199 denture base resin (Group I), GC supersoft (Group II) and Permasoft (Group III) softliners. The samples from Group I, II and III were further divided into 3 sub groups and each sub group had 10 samples each [Table/Fig-1]. The sub grouping was based on the type of surface produced by the machining. In which Sub Group A was control Group that is smooth produced against the glass. Sub Group B was produced by machining with the tungsten carbide bur and Sub Group C is machined with the stone bur.
Denture base resins and softliners
S. No. | Brand Name | Manufacturer | Composition | Powder Liquid Ratio |
---|
1 | Lucitone 199 | DENTSPLY international Inc | Polymethyl methacrylate, methyl methacrylate, benzoyl peroxide, Glycol dimethacrylate | 21gm/32cc powder to a 10ml of liquid |
2 | GC supersoft soft liner | GC America | Polyethyl methacrylate, methacrylate ester, and a phthalate ester plasticizer. | 5gms of powder to a 4ml of liquid. |
3 | Permasoft softliner | DENTSPLY international Inc | Polyethyl methacrylate, methacrylate ester, and a phthalate ester plasticize | 10cc/6.5gm of powder to 4cc of liquid |
Sample Preparation
Samples measuring 15 ×15 mm were cut from 1.5mm thickness red modeling wax [5]. Each sample was mounted onto a cover slip.
Preparation of the mold: Mounted cover slip was embedded in an investing medium that was die stone in the lower half of the flask. After the investing material hardens it was coated with an agent, such as sodium alginate, to prevent the stone or plaster mixture that is poured into the upper half of the flak from adhering to that in the lower half. The investment material was poured into the upper half of the flask. Five samples were flasked in each flask. As soon as the stone was set, flasks were separated, and the wax was removed.
Polymerization of acrylic resin and soft liners was performed in strict compliance with the manufacturer’s instructions [Table/Fig-1]. The flask with denture base resin (Lucitone 199) was submerged in water at room temperature, and rise the temperature to 163oF/ 72oC for 90min, followed by 30min in boiling water. Flask was bench cooled for 30min at room temperature and then in cool water for 15min and deflasking was done. Total 30 samples were prepared by following the same procedure. The flask with GC supersoft soft liner was placed in hot water of 165of/74oC for approximately 30min and slowly temperature was increased to boiling point for 30min and placed for 10min. Deflasking was done. Total 30 samples were prepared by following the same procedure. Permasoft soft liner polymerized at 212oF/100oC for 15min and deflasking was done. Total 30 samples were prepared by following the same procedure.
Machining of Samples
All specimen surfaces except control group (which is smooth produced against the glass) were machined with tungsten carbide bur and stone bur [Table/Fig-2]. The procedure for machining the surface was standardized by ensuring the rotary instrument was cutting only along the surface of sample in one direction. Speed of hand piece (Marathon Multi 600; Model SDE–S60/L60) was controlled at 15,000rpm. Minimal pressure was used, as would be the case in clinical practice when making fine adjustments to the surface of a denture base [10].
S. No. | Type | Manufacturer | Bur No. |
---|
1 | Tungsten carbide bur | DENTSPLY international Inc | 406901 |
2 | Stone bur | DENTSPLY international Inc | 192 |
Scanning Electron Microscopy
After machining, all the samples were mounted on aluminum stubs and were sputter coated with gold (HITACHI HUS-GB under vacuum). All samples were viewed by SEM (Hitachi S-520, Hitachi F-300N) at 0 degree and 45 degree tilt (accelerating voltage was 10 kV) and the magnification was standardized (×50, ×200, xl000). Representative areas of each surface of one set of samples (Lucitone, GC SUPER soft and PERMASOFT) were soft copied at both angles of tilt and at the three chosen magnifications. The ten samples were stabilized and fixed than the samples were viewed and, for purposes of comparison. The photomicrograph was taken for all the specimens which included all the three surfaces of each group were recorded at a magnification of (x200). The same procedure was followed for remaining specimens.
Surface Roughness Calculation
Surface roughness calculated manually without contacting the surface. 10 unit scales as given in the SEM photomicrograph. Since 1unit is equal to 10μm, based on this, the photomicrograph was divided vertically and horizontally, so that each square box surface area (S2) was 20μm. The number of pits in given square was counted which gave the roughened surface area of that particular specimen. Average roughness (Ra) values for each profile were thus calculated. An analysis of variance (ANOVA) with the Tukey’s HSD test was used to compare Ra of the individual surfaces.
Results
The machined surfaces can be directly compared, the SEM photomicrographs to the surface profile tracings considered representative of the surface with the Ra measurements lying within a 0.5 standard deviation of the mean. All surface profiles were recorded by using a standardized method with a total profile length of 270μm.
Group I (Lucitone 199)
Examination of the acrylic resin showed a smooth surface against glass [Table/Fig-3], which was used as a control. The surface machined by stone bur [Table/Fig-4] had a more evenly textured surface than the surface machined by the tungsten carbide bur [Table/Fig-5].
SSEM photomicrographs of Lucitone 199 showing smooth surface against glass (original magnification x1000)
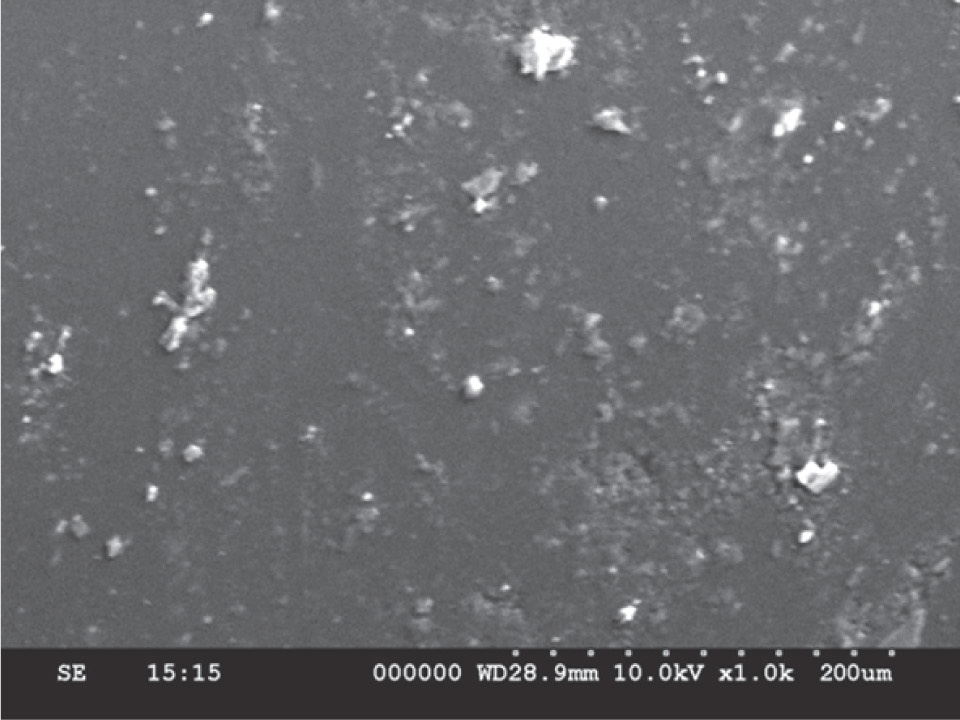
SEM photomicrographs of Lucitone 199 showing the surface produced by the stone bur (original magnification x250)

SEM photomicrographs of Lucitone 199 showing the surface produced by the Tungsten carbide bur (original magnification x250)
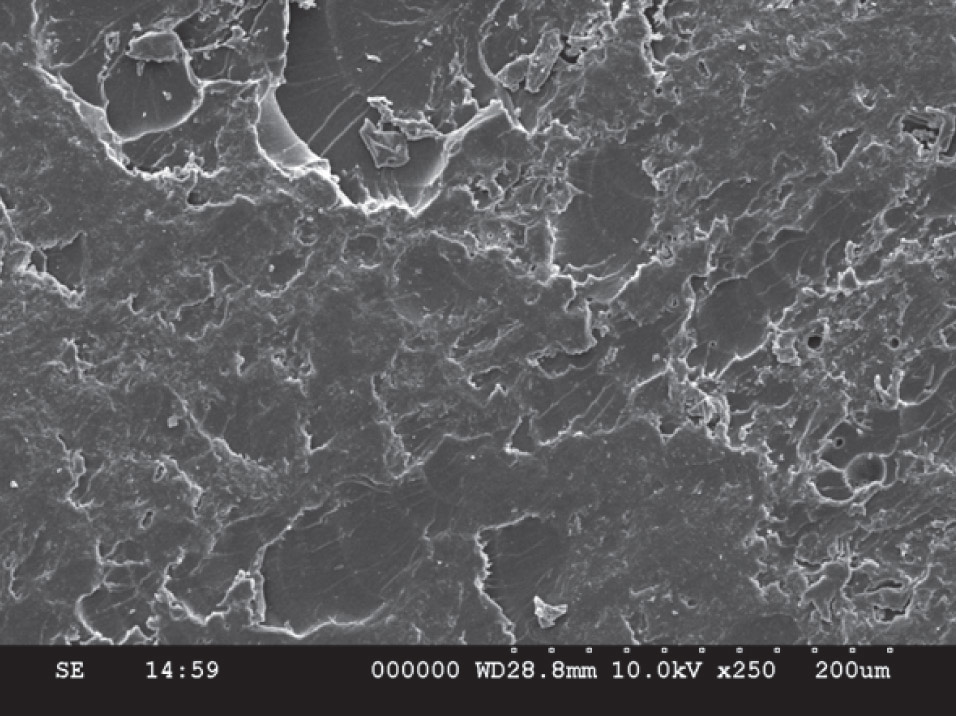
The surface produced by the tungsten carbide bur appears to be smooth but average surface roughness is more than the surface produced by the stone.
Group II (GC Super Soft – Soft Liner)
The profile of GC Super soft machined by a tungsten carbide bur [Table/Fig-6] showed smoother surface than the surface produced by a stone bur [Table/Fig-7]. GC Super soft processed against glass [Table/Fig-8] had an average roughness of 0.059774μm; when machined by the stone bur, the Ra was 2.6μm; and, when machined by the tungsten carbide bur, it was 1.617097μm.
SEM photomicrographs of GC Super soft softliner showing the surface produced by Tungsten carbide bur (original magnification x250)
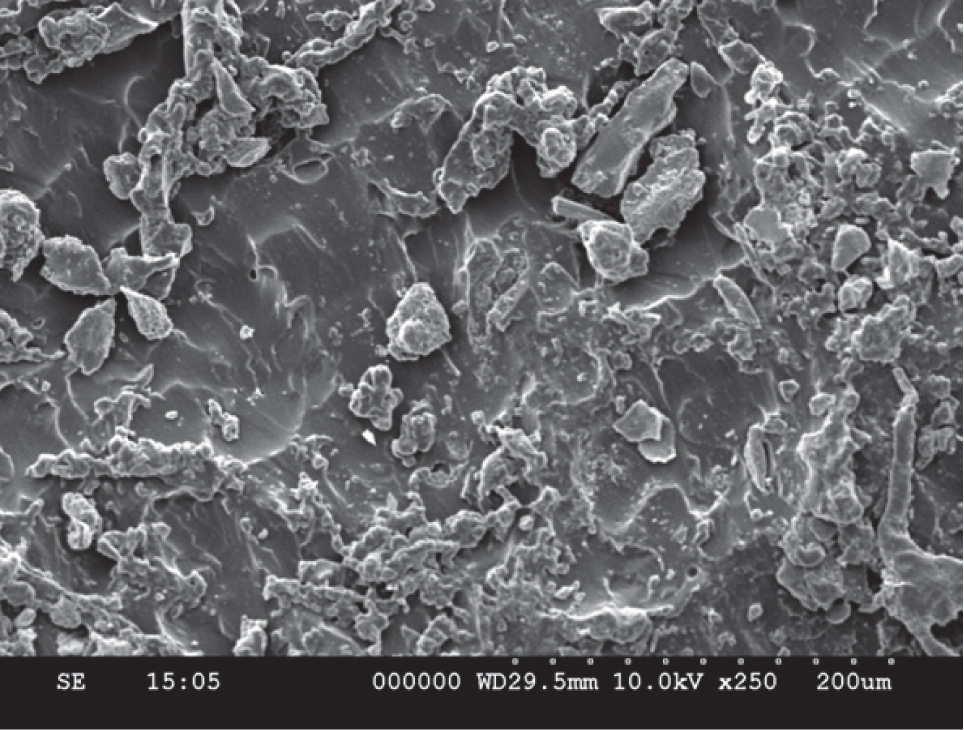
SEM photomicrographs of GC Super soft softliner showing the surface produced by the stone bur (original magnification x250)
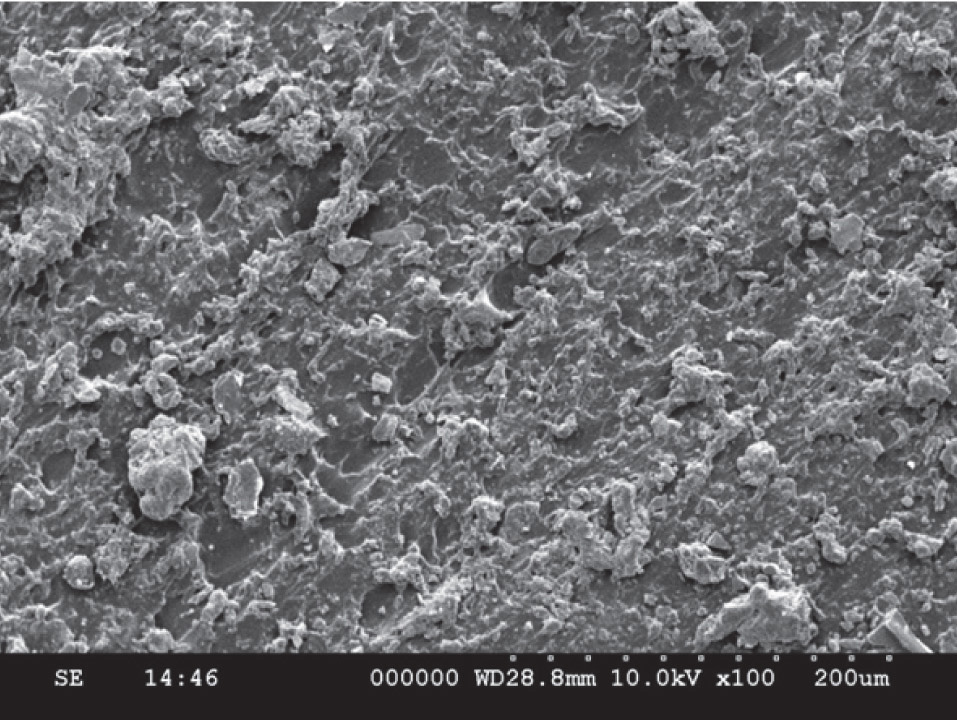
SEM photomicrographs of GC Super soft softliner showing smooth surface produced against glass (original magnification x1000)
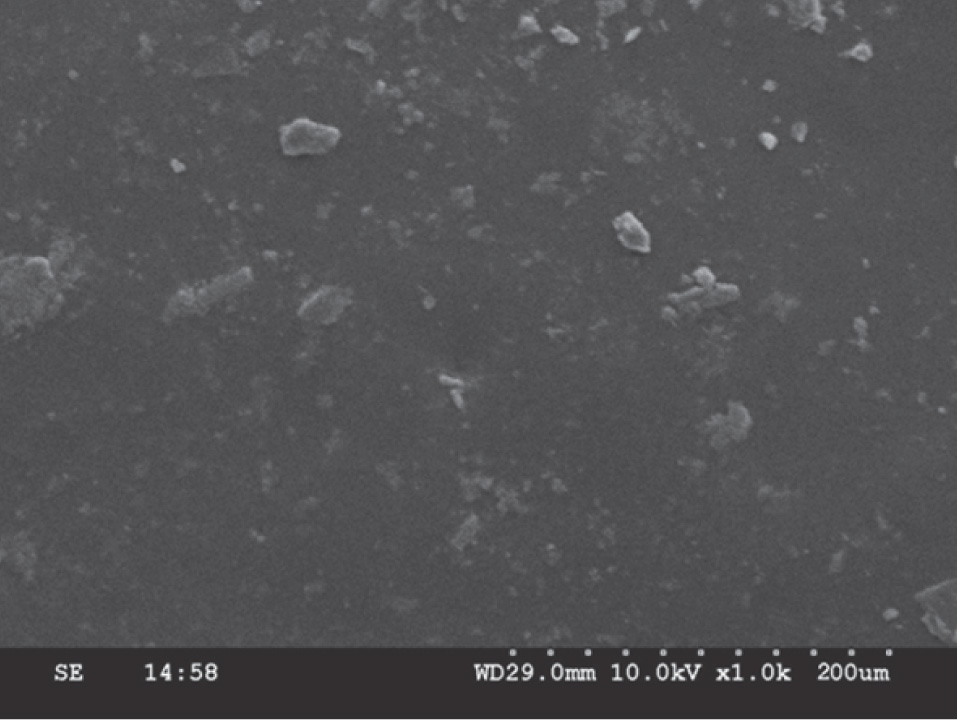
Group III (Permasoft Soft Liner)
As with the previous two materials a smooth surface was produced against glass [Table/Fig-9]. The surface machined by the tungsten carbide bur produced the smoothest for the entire surface on the soft lining materials [Table/Fig-10,11].
SEM photomicrographs of Permasoft softliner showing smooth surface produced against glass (original magnification x1000)
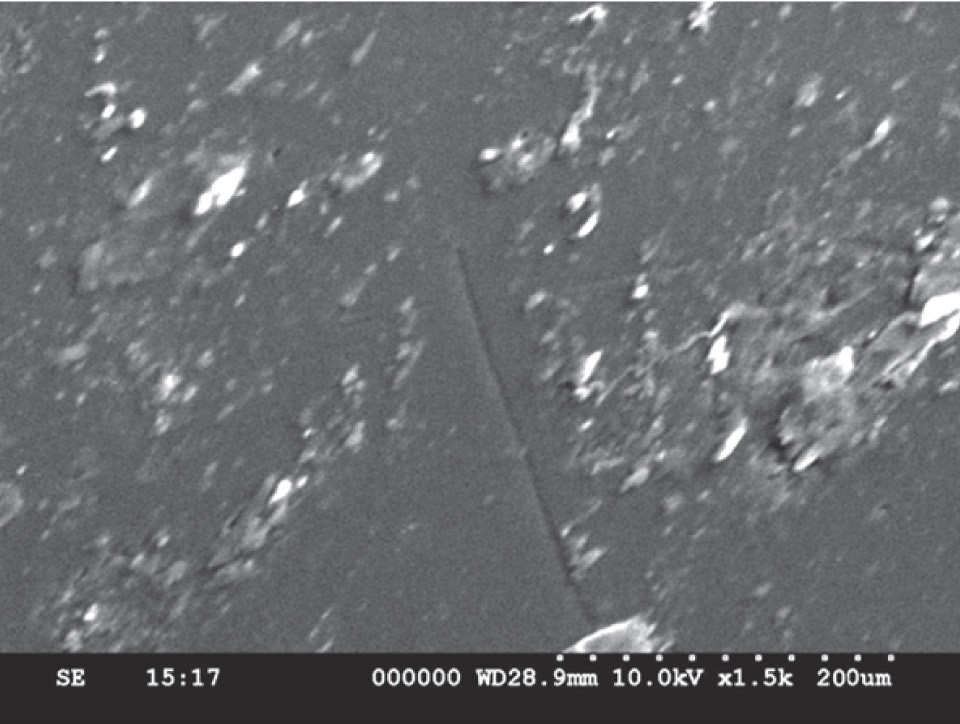
SEM photomicrographs of Permasoft softliner showing the surface produced by Tungsten carbide bur (original magnification x250)
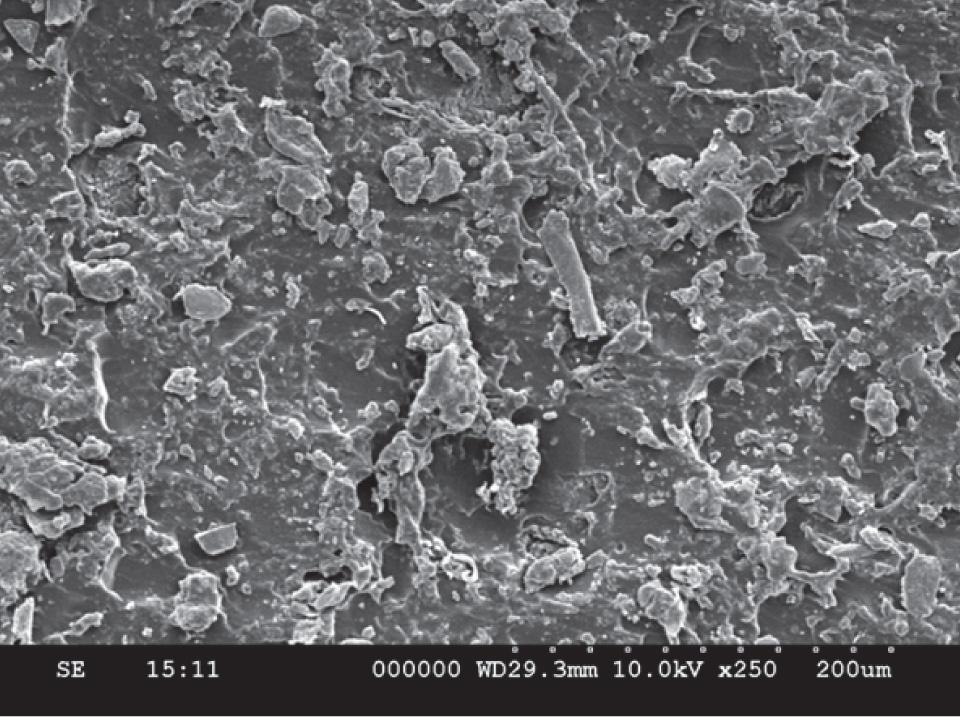
SEM photomicrographs of Permasoft softliner showing the surface produced by the stone bur (original magnification x250)
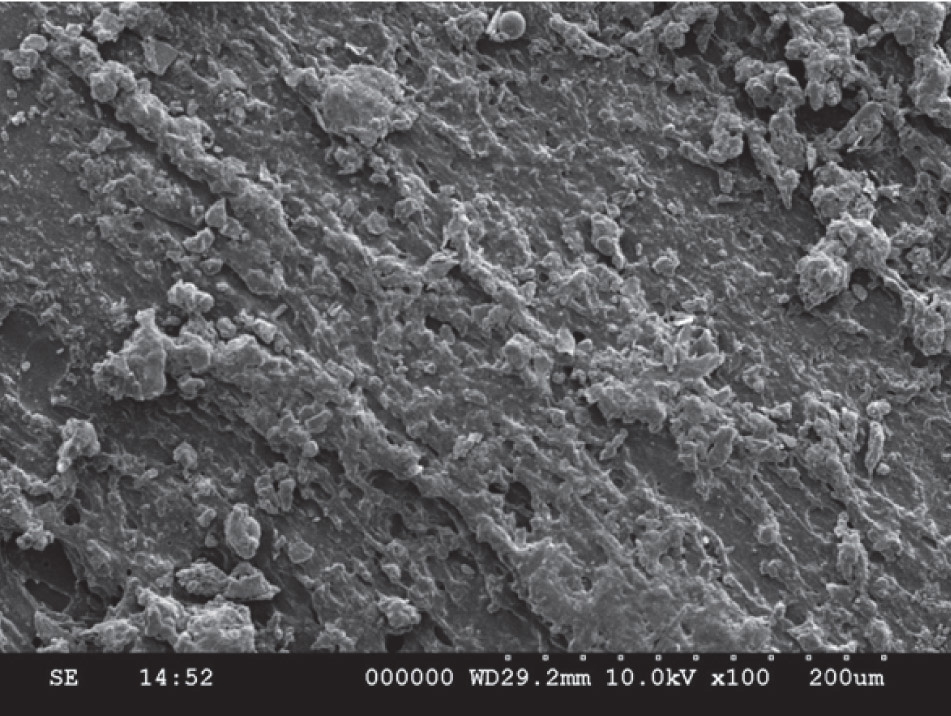
Discussion
This study was done to evaluate the effect of surface machining with two commonly used denture trimming burs on the commonly used denture base resin (Lucitone 199) and two softliners (GC supersoft and Permasoft).
A smooth surface finish to denture base materials is desirable, as mucosal irritation has been attributed to rough surfaces. However, more importantly rough [10,12,13], nonshedding surfaces in vivo have been shown to accumulate more plaque than smooth surfaces [9,10]. The ability to achieve a smooth surface on adjusted fit surfaces depends on the machining properties of the material itself, the instruments used, and the time that can be spent in achieving the required finish [10].
Verran J and Christopher [12] found that yeast cells like Candida albicans will retain more on the rougher surfaces than the smoother surfaces. The fitting surface of the denture can act as a reservoir of Candida albicans in denture stomatitis [11]. Tsun Ma [14] stated that surface roughness is also prerequisite for discoloration of denture base resins due to retention of the stains.
Evaluation of the surface characteristics of acrylic denture base resins with the help of Scanning Electron Microscope at various magnifications has been acknowledged by various researchers. Kuhar M [5] evaluated the effects of various polishing techniques on the surface roughness of both autopolymerized and heat cured denture base resins by using scanning electron microscope.
The SEM photographs of Lucitone 199 showed that smooth surface with the Ra value 0.6581μm was produced against the glass which was the control group [Table/Fig-3]. The surface machined by the stone bur [Table/Fig-4] had a series of narrow grooves in the direction of machining with irregular small pits, whereas tungsten carbide bur produced a surface with large irregular pits [Table/Fig-5]. The surface produced by the carbide bur appears to be smooth, but from the surface profile graph, the carbide surface is more rougher than the stone surface with average surface roughness Ra 5.3881μm [Table/Fig-12], whereas surface roughness of stone bur was Ra 3.6681μm. Similar study conducted by the Radford DR [10] on heat cure acrylic denture base resin with tungsten carbide bur and steel bur. In their study they found that the tungsten carbide bur produced a smoother surface than the steel bur.
Average roughness (Ra) values of control and machined surfaces (n = 30 of each group), Average surface roughness measurements (Ra) (n = 10 of each surface)
Material | Surface | Mean Ra values (um) ±Standard deviation | p-values |
---|
Group I (Lucitone199) | Smooth | 0.6581±0.2615 | <0.0001 |
Carbide | 5.3881±0.3373 |
Stone | 3.6681±0.254 |
Group II (GC supersoft softliner) | Smooth | 0.059774±0.35654 | <0.0001 |
Carbide | 1.617097±0.191767 |
Stone | 2.6±0.1625 |
Group III (Permasoft softliner) | Smooth | 1.684839±0.20268 | <0.0001 |
Carbide | 2.237419±0.354259 |
Stone | 4.184839±0.409869 |
Large positive cutting rake angles of the blades and polished tool faces are recommended for machining of plastics. Another factor that will affect the surface character produced by the bur is the number of its cutting edges, which contact the substrate in unit time for a given rate of speed of the instrument [10]. The tungsten carbide bur had its cutting edges in the form of a diamond, whereas the stone bur in the form of sand paper with grit size of 100. Both burs generated grooves, although those made by the stone bur were barely visible. Berger JC [15] conducted a study on surface roughness of Lucitone 199 and other denture base resins, produced by conventional polishing and chair side polishing, there was no significant difference between these procedures.
Tungsten carbide bur produced a smooth surface on the GC super soft and Permasoft softliners, with Ra values of 1.617097μm and 2.237419μm. Particularly rough surfaces resulted from the use of the stone bur on the two soft lining materials with Ra values of 2.6μm and 4.184839μm. Scratches like grooves in the direction of movement of the stone bur were noticeable on the machined surfaces. These could have resulted either from a sharp grinding grits or trapped fractured particles that pass over a tooth of the bur. Smoother surfaces could have been achieved by using a different grade of stone bur that has smaller particles; however, this would have increased the risk of clogging the bur with particulate material.
Plastics are soft and require little energy to cut, but difficulties stem from their low thermal conductivity, high coefficient of thermal expansion and low elastic modulus. The first of these difficulties has particular relevance when machining denture bases as low thermal conductivity can produce over heating of the material surface. If the glass transition temperature is reached, surface smearing is likely to result. The glass transition temperature for polymethyl methacrylate is between 105oC and 115oC [10].
Finishing long term, resilient liner materials generally is difficult because of their resilience: the materials tend to pull when adjusted with stone bur. Moreover, liner materials have a lower glass transition temperature than hard acrylic resin; if liners are subjected to too much pressure, generated heat may soften and distort the material [4]. This may result in rougher surface than the tungsten carbide bur.
Conclusion
With in the limitations of this in vitro study, the following conclusions were drawn:
Stone bur produced smoother surface on Lucitone199 than the tungsten carbide bur.
Tungsten carbide bur produced a smoother surface on the GC super soft and Permasoft softliners.
Among the three groups, tungsten carbide bur produced the smoothest surface on GC supersoft sofliner.
These results can have a significant clinical implication. While using Lucitone 199 stone bur can be used for chair side adjustments. Carbide bur can be used for GC supersoft and Permasoft softliners to achieve smoother surface.