In the modern era, there has been an increase in the application of ceramics in dentistry and biomedical fields. Martin Heinrich Klaproth accidentally discovered zirconium dioxide (ZrO2) in 1789 while working with gems [1]. In 1969, zirconium oxide (ZrO2) was first used for medical purposes in orthopaedics, replacing aluminum or titanium for femoral head replacement [1]. Recently, Y-TZP ceramics (Yttrium-stabilised Tetragonal Zirconia Polycrystalline) have gained popularity due to their superior mechanical, aesthetic, and biocompatibility properties compared to conventional dental ceramics [1].
Zirconia Veneered with feldspathic Porcelain (ZVP) offers better aesthetics, while MZ provides greater strength [2]. Fracture and chipping of the veneering layer are common clinical complications associated with ZVP. MZ restorations do not require veneering with aesthetic materials, thereby eliminating the chipping problem [2].
Zirconia can exist in three allotropic forms. At room temperature and up to 1170°C, the monoclinic (m) structure is observed. Upon heating between 1170°C and 2370°C, the tetragonal (t) structure appears. The cubic (c) structure is formed when heated above 2370°C and upto its melting point [2]. The metastable tetragonal phase is stabilised by incorporating oxides such as CaO, MgO, Y2O3, or CeO2 into pure zirconia. The phase transformation from tetragonal to monoclinic can be induced by temperature changes, stress, or surface treatments. This phase transformation results in an increase in volume that slows and halts crack propagation by forming a compressive layer, thus enhancing fracture toughness [3].
Currently, Computer-aided Design (CAD)/Computer-aided Manufacturing (CAM) applications for zirconia include the fabrication of veneers, full coverage crowns, Fixed Partial Dentures (FPDs), implants, and customised abutments. The fabrication of zirconia restorations is done either by soft machining of pre-sintered blanks or hard machining of fully sintered blocks. Restorations obtained through soft machining must be sintered after all formation steps are completed. After sintering, a superficial treatment known as glazing is applied to zirconia surfaces, which enhances their appearance, making them look more like natural teeth. Glazing seals any open pores on the surface, resulting in a smooth finish with good optical properties [4].
The benefit of glazing ceramics is that it may increase fracture resistance and reduce potential abrasiveness. In the majority of cases, it is essential to make adjustments to occlusion, interproximal contacts, and axial contour during the intraoral trial of the final prosthesis. In common practice, fine-grained diamond burs are used to modify or adjust the zirconia surfaces. However, these adjustments disrupt the glaze layer, and if the surface of the restoration is left rough, it can lead to plaque accumulation, dental caries, gingival inflammation, periodontal problems, and abrasion of opposing teeth [3].
Thus, an abraded surface should be either polished or reglazed. However, reglazing requires an additional clinical session. Numerous finishing and polishing systems are available in the market for zirconia restorations, such as diamond rotary instruments of different sizes and shapes, as well as silicone cups, points, and wheels that are diamond-impregnated and made from natural or synthetic diamond grit grades [4,5]. Huh YH et al., found that various zirconia polishing systems significantly smoothed surfaces compared to other systems, but it was also noted that all systems were clinically acceptable [6]. The use of a ceramic polishing kit ensured a smooth surface, yielding durable and cost-effective outcomes [7]. Therefore, chairside polishing of the prosthesis can be performed, which is supported by several studies stating that polishing is a good alternative to reglazing [8,9]. However, various studies also suggest that reglazing is superior. This remains a controversial topic, with various authors expressing differing opinions when comparing glazing and polishing.
In a study conducted by Papanagiotou HP et al., it was observed that the polishing procedure helps increase the strength of dental ceramics and reduces surface roughness [10]. It was also found that there is a negative correlation between surface roughness and zirconia strength [11].
It is a known fact that grinding zirconia has two counteracting effects: it can either produce surface compressive stress that enhances crack healing and increases the strength of the material through transformation toughening, or it may induce surface flaws that exceed the depth of the compressive layer, potentially decreasing the strength of the material [12]. There is still controversy regarding the effects of grinding, polishing, and glazing on the properties of zirconia [3,11,13-15]. Thus, the present study was conducted to investigate the effects of the proposed polishing or surface restoration method on the strength and surface roughness of the restoration.
The null hypothesis states that there are no differences in mean roughness or flexural strength among ground, polished, and glazed MZ, and that there is no correlation between flexural strength and roughness.
Materials and Methods
This in-vitro study was conducted in the Department of Prosthodontics at MM College of Dental Sciences and Research in Mullana, Haryana, India, from April to December 2019. Ethical clearance was obtained from the Institutional Ethical Committee (IEC 1923). In present study, 32 bar-shaped samples were fabricated.
Study Procedure
A total of thirty-two standardised MZ blocks [Table/Fig-1] were constructed from presintered high-translucent MZ blanks (NexxZr T, Sagemax) using CAD/CAM technology. The composition of the material is as follows: ZrO2 ≥89%, Y2O3 4-6%, HfO2 ≤5%, and Al2O3 <1%. The length, width, and thickness of each zirconia block were maintained at 20 mm, 5 mm, and 3 mm, respectively, in accordance with American Dental Association (ADA) Specification Number 69. The blocks were then sintered according to the manufacturer’s instructions. The dimensions of the samples were checked using a digital caliper, after which each specimen was glazed in a ceramic furnace.
Monolithic Zirconia (MZ) blank.
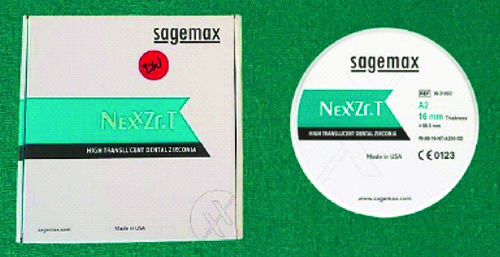
Grouping of specimens: A total of 32 specimens were fabricated and divided into four groups, with each group consisting of eight specimens [Table/Fig-2].
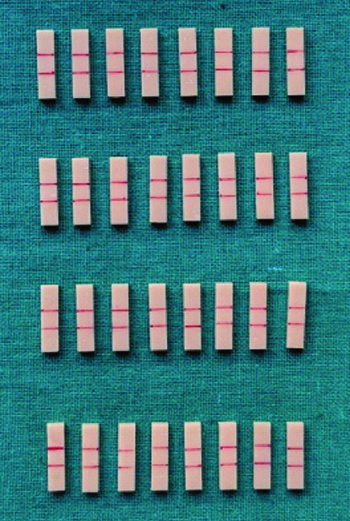
Group C- Glazed (Control)
Group G- Grinded
Group GR- Grinded and Reglazed
Group GP- Grinded and Zirconia Polishing Kit
Group C- There are eight glazed samples that were kept as a control, meaning they were not ground. The remaining 24 samples were ground to simulate the adjustments made in a clinical setting.
Grinding procedure: Bars were marked at 5 mm intervals at the center of each specimen. Grinding was performed for 20 seconds with a 10-second interval, using a sweeping motion with a 40-grit diamond point (TR-25F, Mani Inc, Japan) and an air rotor handpiece with water coolant to simulate adjustments in a clinical setting. The diamond point was changed after every five samples. Grinding was conducted by a single operator. The samples were then ultrasonically cleaned for 15 minutes. After cleaning, the samples were treated according to their respective groups.
Group G- Eight ground samples were ultrasonically cleaned for 15 minutes and then air-dried.
Group GR- Eight samples were subjected to reglazing according to the manufacturer’s instructions. A layer of glaze (IPS Ivocolour, Ivoclar, USA) was applied to the ground surface, and the specimens were fired at a temperature of 900°C without vacuum, following the manufacturer’s instructions.
Group GP- The ground surfaces of the eight specimens were polished using a Zirconia polishing kit (Kenda Zircovis Diamond, Liechtenstein) [Table/Fig-3]. Polishing was performed in two steps with a diamond-impregnated polisher that had two rotary points: a blue rubber (medium) and a red rubber (fine) polisher, operated at low speed for two minutes. First, the medium grit polisher was used for one minute at 10,000 rpm. Thereafter, the fine grit polisher was used for another one minute at the same speed [Table/Fig-4]. Polishing was conducted in a sweeping motion, moving both forward and backward. The samples were then cleaned ultrasonically for 15 minutes in distilled water and air-dried.
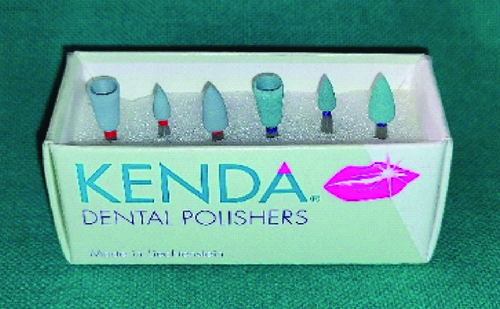
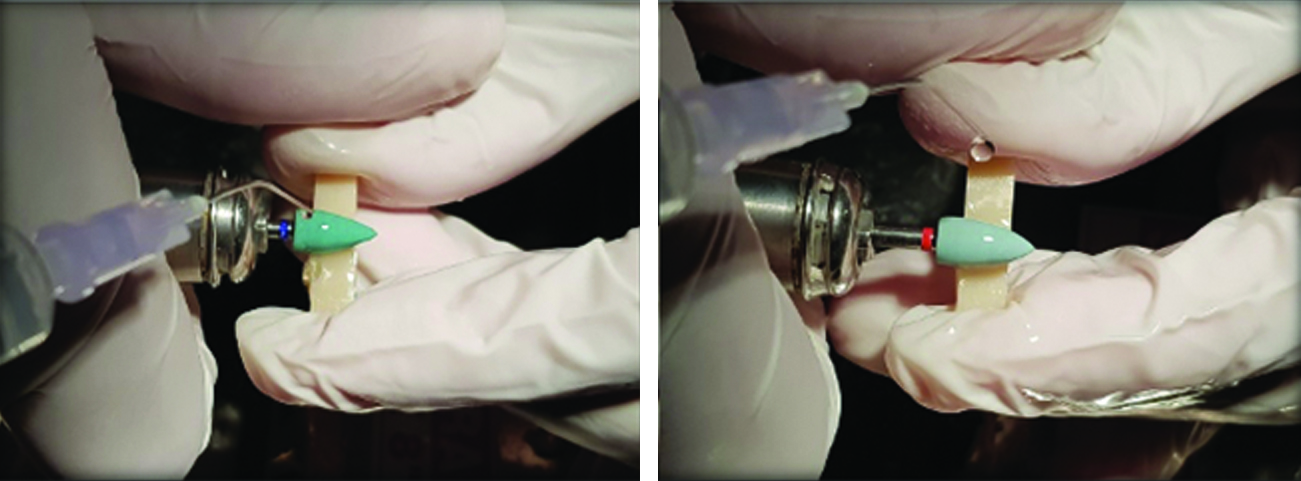
Surface roughness evaluation: The surface roughness of the specimens was measured using a profilometer. Ra was the parameter calculated during the test, which was conducted using a physical probe that traced the surface. Ra represents the surface roughness and is calculated as the average roughness of the surface, measured by the microscopic spikes and valleys during the stylus tracing. The profilometer determines the roughness of the specimen surface, and Ra can be described as the arithmetical average of all absolute distances of the surface profile from the centerline within the measuring length [Table/Fig-5].
Surface roughness evaluation.
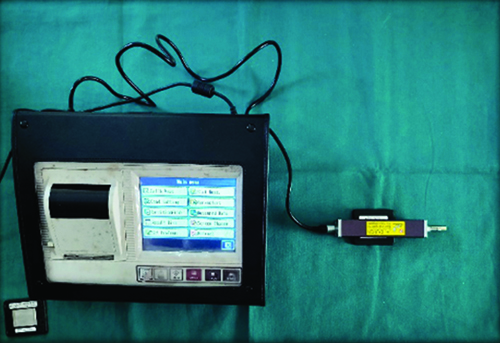
A pick-up with a diamond stylus (5 μm tip radius) was used under a constant pressure force of 4 mN, with a tip angle of 90 degrees. Calibration of the instrument was performed using a standard reference specimen (ISO 1997) at a speed of 0.5 mm/s and a traversing length of 0.25 mm.
The surface roughness of each sample was measured at three locations to obtain the mean surface roughness. The surface roughness of the ground, reglazed, and chairside polished surfaces was recorded. For each sample, the stylus was run in three different directions: horizontally, vertically, and obliquely. This method was consistently applied to obtain three values for each sample. A larger Ra value indicates greater surface roughness, while a lower Ra value signifies a smoother surface.
Flexural strength evaluation: Flexural strength was determined using a 3-point bending test conducted on a Universal Testing Machine (UTM) at a crosshead speed of 0.5 mm/min, with a span length of 15 mm [Table/Fig-6]. The maximum load that caused the fracture of the specimen was recorded. The mean fracture strength was calculated using the following formula, as recommended by the ISO 6872 standard, 1995.
Universal Testing Machine (UTM) for flexural strength evaluation.
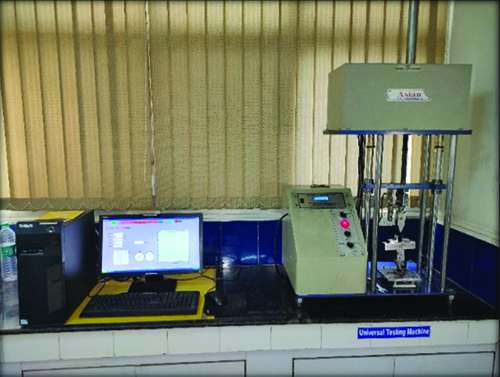
M=3WI/2bd2 [16]
M=Flexural strength (Mpa)
W=Fracture load (N)
I=Distance between support points (mm)
B=Breadth of specimen (mm)
D=Thickness of specimen
Statistical Analysis
The statistical analysis was conducted using One-way ANOVA, HSD post-hoc test, and Pearson’s correlation to analyse the mechanical properties of zirconia. The analysis was performed using IBM SPSS Statistics version 25.0 (Armonk, USA). A p-value of less than 0.05 was considered statistically significant.
Results
The mean and standard deviation of the surface roughness (Ra) for all four groups were calculated. Group C, the control group (0.4403), demonstrated the minimum value for surface roughness, followed by Group GP (Polished) at 0.656, Group GR (Reglazed) at 0.809, and Group G (Ground) specimens, which exhibited the maximum value at 1.467 [Table/Fig-7].
Mean surface roughness (Ra) and standard deviation of specimens according to different surface treatments.
Groups | Mean±SD | Maximum | Minimum |
---|
Control (C) | 0.4403±0.096 | 0.58 | 0.30 |
Ground (G) | 1.467±0.327 | 2.03 | 1.02 |
Ground and Glazed (GR) | 0.809±0.215 | 1.19 | 0.56 |
Ground and Polished (GP) | 0.656±0.163 | 0.84 | 0.38 |
In the intergroup analysis, statistically significant differences were found between Group C and Group G (p<0.01), Group C and Group GR (p=0.01), Group C and Group GP (p=0.008), Group G and Group GP (p<0.01), and Group G and Group GR (p<0.01). However, there was no statistically significant difference between Group GP and the other groups (p=0.53) [Table/Fig-8].
Intergroup analysis of surface roughness (Ra) of specimens according to groups.
Tukey’s HSD post-hoc test |
---|
Groups | Mean difference | 95% CI | p-value |
---|
Control (C) vs Ground (G) | 1.03 | 0.7317 to 1.3283 | <0.01* |
Control (C) vs Ground and Glazed (GR) | 0.37 | 0.0717 to 0.6683 | 0.01* |
Control (C) vs Ground and Polished (GP) | 0.22 | -0.0783 to 0.5183 | 0.008* |
Ground (G) vs Ground and Glazed (GG) | -0.66 | -0.9583 to -0.3617 | <0.01* |
Ground (G) vs Ground and Polished (GP) | -0.81 | -1.1083 to -0.5117 | <0.01* |
Ground and Glazed (GR) vs Ground and Polished (GP) | -0.15 | -0.4483 to 0.1483 | 0.53 |
*:statistically significant (p<0.05)
When assessing the flexural strength (MPa) of all four groups, it was found that the reglazed zirconia sample (Group GR) had the highest flexural strength value at 599.859 MPa, followed by Group C at 524.043 MPa [Table/Fig-9].
Mean Flexural Strength (MPa) and Standard Deviation of specimens according to different surface treatments.
Groups | Mean | SD | Minimum | Maximum |
---|
Control (C) | 524.043 | 56.834 | 428.06 | 605.56 |
Ground (G) | 478.809 | 99.951 | 355.98 | 657.05 |
Ground and Relazed (GR) | 599.859 | 57.371 | 486.41 | 651.65 |
Ground and Polished (GP) | 491.864 | 87.773 | 358.93 | 592.32 |
In the intergroup analysis of flexural strength, no statistically significant differences were found between Group C and Group G (p=0.66), Group C and Group GR (p=0.23), or Group C and Group GP (p=0.84). However, a statistically significant difference was observed between Group G and Group GR (p=0.02), as well as between Group GR and Group GP (p=0.04) [Table/Fig-10].
Intergroup analysis of flexural strength (MPa) of specimens according to groups.
Tukey’s HSD post-hoc test |
---|
Group | Mean difference | 95% CI | p-value |
---|
Control (C) vs Ground (G) | -45.23 | -151.45 to 60.99 | 0.66 |
Control (C) vs Ground and Glazed (GR) | -75.82 | -30.39 to 182.04 | 0.23 |
Control (C) vs Ground and Polished (GP) | -32.18 | -0.078 to 0.518 | 0.84 |
Ground(G) vs Ground and Glazed (GR) | 121.05 | -0.958 to -0.362 | 0.02* |
Ground (G) vs Ground and Polished (GP) | 13.05 | -1.108 to -0.512 | 0.98 |
Ground and Glazed (GR) vs Ground and Polished (GP) | -108.00 | -0.448 to 0.148 | 0.04* |
*:statistically significant (p<0.05)
The correlation between surface roughness and flexural strength was assessed using Pearson’s correlation analysis [Table/Fig-11]. A weak positive linear relationship was found in the Ground and Reglazed groups. Overall, a significant relationship was established.
Pearson correlation between surface roughness and flexural strength.
Pair | r value | p-value |
---|
Control (C) (Surface Roughness) and Control (C) (Flexural strength) | -0.13 | 0.77 |
Ground (G) (Surface Roughness) and Ground (G) (Flexural strength) | 0.12 | 0.79 |
Ground and Glazed (GR) (Surface Roughness) and Ground and Glazed (GR) (Flexural strength) | 0.35 | 0.39 |
Ground and Polished (GP) (Surface Roughness) and Ground and Polished (GP) (Flexural strength) | 0.22 | 0.60 |
Overall | -0.1 | 0.58 |
Discussion
In the present study, no correlation was found between flexural strength and roughness; however, the type of surface restoration did impact the surface roughness and flexural strength of MZ. The results revealed that occlusal adjustments significantly influenced surface roughness values. Surface roughness values (Ra) increased with grinding and decreased with polishing. Therefore, the null hypothesis- that there are no differences in mean roughness or flexural strength among the ground, polished, and reglazed samples, and that there is no correlation between flexural strength and roughness- was partially rejected.
Sabrah AH et al., evaluated the wear behaviour and surface roughness of polished, glazed, and ground MZ [17]. Their findings revealed that although glazed zirconia has a smoother surface, it is not preferred over unglazed MZ. Heintze SD et al., found that glazed surfaces (glazed at 820°C for two minutes) cause more wear to the opposing tooth than polished surfaces (polished in a two-step procedure with a zirconia polishing kit for 60 seconds) [18]. Thus, while reglazing results in greater smoothness, its longevity cannot be established when the restoration is in function. Therefore, appropriate polishing can reduce antagonist abrasion.
In present study, a high-speed handpiece was used to grind the specimens under water cooling. A similar procedure was followed in the studies by Hmaidouch R et al., Chougule KJ et al., and Aboushelib MN and Wang H, [3,16,19]. To standardise the parameters, all surface treatments were conducted by the same operator. Surface roughness was evaluated using a profilometer, as employed by Mohammadi-Bassir M et al., Caglar I et al., and Azeez SM and Salih SA, [8,20,21]. The contact profilometer used in present study is advantageous for its accuracy, being less influenced by surface material properties such as colour or transparency compared to non contact profilometers.
In the present study, ground samples exhibited the highest surface roughness (1.467 μm), while polishing (0.656 μm) and reglazing (0.809 μm) reduced roughness, with the smoothest surface observed in the control group (0.4403 μm). The results of present study are consistent with the findings of Mohammadi-Bassir M et al., and Khayat W et al., who also reported greater roughness in ground zirconia compared to the reglazed and polished groups [8,22]. Various equipments can be used for surface characterisation, including profilometers, mechanical surface roughness testers, Scanning Electron Microscopy (SEM) for morphological characteristics, and total reflection Fourier-transform infrared spectroscopy for surface chemical composition.
Azeez SM and Salih SA, found that polished zirconia was smoother than reglazed zirconia, which is consistent with our findings [21]. Hmaidouch R et al., Mitrov G et al., and Janyavula S et al., also reported lower surface roughness with polishing compared to glazing [3,23,24]. However, Sabrah AH et al., found different results, likely due to variations in polishing and glazing techniques or study protocols, as noted by Özkurt-Kayahan Z [17,25]. Polishing often yields better results because it may remove loosely attached surface grains and grinding trace lines, as highlighted by Dupriez ND et al., [26]. Anusavice KJ noted that polishing might be more effective than reglazing due to the insufficient thickness of the glaze to fill micro-cracks and grooves [27].
Studies by Aboushelib MN and Wang H, and Al-Haj Husain N and Ozcan M, indicate that abrading introduces compressive stress, hindering crack propagation and increasing flexural strength, possibly due to a phase transformation of zirconia from tetragonal to monoclinic [19,28]. However, Iseri U et al., Khayat W et al., and Al-Haj Husain N et al., found that grinding reduces zirconia’s strength [12,22,28]. In present study, the mean flexural strength after grinding (478.809 MPa) was lower than that of the control group (524.043 MPa), though the difference was not statistically significant, likely because the surface flaws resulting from grinding exceeded the depth of the compressive layer.
The flexural strength of the control group (524.043 MPa) was lower compared to that of the reglazed group (599.859 MPa), although the difference was not statistically significant, similar to the findings by Chougule KJ and Wadkar AP, [16]. The increase in flexural strength in the reglazed group may be attributed to the reglaze layer filling surface flaws and creating compressive stress upon cooling, thereby enhancing strength. Polishing increased the flexural strength of abraded MZ specimens, consistent with studies by Mohammadi-Bassir M et al., and Aboushelib MN and Wang H, although not statistically significant [8,19]. Traini T et al., found that fine polishing reduced surface roughness but also decreased fracture toughness and induced microcracks, similar to our findings, where the polished group (491.864 MPa) exhibited a lower mean flexural strength than the control group [29]. Guazzato M et al., explained that polishing might remove the monoclinic phase and the layer of compressive stress, thereby reducing flexural strength [30]. Nakamura Y et al., found that the flexural strength of the reglazed samples was the highest when compared with polished samples, consistent with our study [31]. However, Kumchai H et al., found that external glazing decreased flexural strength [9]. Findings from similar studies in the literature are presented in [Table/Fig-12] [8,16,21-24,29,31].
Discussion of various studies from the literature [8,16,21-24,29,31].
Author’s name and year | Place of study | Number of subjects | Materials compared | Parameters assessed | Conclusion |
---|
Chougule KJ and Wadkar AP, 2017 [16] | Maharashtra | 30 | 1. No alteration2. Grounded and polished3. Grounded and reglazed | Flexural strength | Reglazing increased the flexural strength compared to polishing |
Azeez SM and Salih SA, 2019 [21] | Iraq | 36 | The control was not modified while the next 27 samples were grinded with a coarse diamond bur and then divided into1. Grinded2. Polished3. Reglazed | Surface roughness | Polished surface showed least surface roughness and glazing restores the smoothness |
Mohammadi-Bassir M et al., 2017 [8] | Iran | 50 | 1. Standard polishing without any surface treatment2. Grinding3. Grinding and overglazing,4. Grinding and polishing with intraoral zirconia polishing kit5. Grinding and polishing with polishing kit | 1. Flexural strength2. Surface roughness | 1. Roughness increased after grinding and reduced equally with polishing and glazing2. Flexural strength significantly decreased after glazing |
Khayat W et al., 2018 [22] | Boston | 44 | 1. Grinding2. Grinding and polishing with Brasseler Zirconia polishing kit3. Grinding and polising with Komet polishing kit4. The control | 1. Flexural strength2. Surface roughness | 1. There was no difference found in the flexural strength2. Grinding increased the surface roughness while polishing decreased the surface roughness |
Mitov G et al., 2012 [23] | Austria | 64 | 1. Polished2. Glazed3. Fine grit diamond grinding4. Coarse grit diamond grinding | Surface roughness | Polishing decreased the surface roughness |
Janyavula S et al., 2013 [24] | Birmingham | 8 | 1. Polished2. Glazed3. Polished and then reglazed4. Veneering porcelain5. Enamel | Surface roughness | Polished surface showed least surface roughness |
Traini T et al., 2012 [29] | Italy | 30 | 1. As received by milling centre2. Coarsely polished3. Fine polished | Surface roughness | Decrease surface roughness was seen with fine polishing |
Nakamura Y et al., 2010 [31] | Japan | 120 | 1. Control (original glazed)2. After grinding with 100 grit3. After grinding with 600 grit4. After grinding with 1000 grit | 1. Surface roughness2. Flexural strength | Glazed surface showed highest flexural strengthAs the surface roughness increased, flexural strength decreased |
Present study | India | 32 | 1. Control2. Grinding3. Grinding and overglazing4. Grinding and polishing with polishing kit | 1. Surface roughness2. Flexural strenrth | Decrease surface roughness was seen with polishingGlazed surface showed highest flexural strength |
There was no overall correlation between surface roughness and flexural strength, consistent with studies by Khayat W et al., and Luthardt RG et al., [22,32]. Hmaidouch R et al., Azeez SM and Salih SA, Mitrov G et al., and Janyavula S et al., demonstrated that chairside polishing is equal to or better than glazing in terms of surface roughness [3,21,23,24], while Chougule KJ and Wadkar AP, argued that glazing is superior [16].
Variations in flexural strength after different surface treatments have been noted by various authors [9,14], likely due to differences in zirconia specimen dimensions. This study followed American Dental Association (ADA) specification no. 69, using medium grit diamond points for clinical adjustments and fine grit diamond points for grinding the glazed surface, which makes direct comparisons difficult. Manual surface grinding and polishing are challenging to standardise; thus, the same operator performed all treatments to minimise variations.
Chairside polishing, which eliminates the need for an extra appointment, can be an effective alternative to reglazing, as it increases zirconia strength post-adjustment. However, if a second visit is possible, reglazing is recommended, as it significantly increases strength compared to polishing.
Limitation(s)
The present in-vitro study utilised fabricated samples (zirconia bars) that may not resemble those used clinically, and therefore, the findings may not accurately reflect real clinical performance. Additionally, the present study focused exclusively on one brand of MZ. For these reasons, the results may not represent what occurs in the oral cavity. Further studies should include various brands of zirconia and different polishing kits to validate the results observed in present research.
Conclusion(s)
Both polishing and reglazing were effective in achieving a smoother surface, with statistically significant findings. However, grinding led to a reduction in the flexural strength of zirconia. Among the surface treatments, the order of effectiveness for achieving smoothness was Control>Polished>Reglazed>Ground, while the order for flexural strength was Reglazed>Control>Polished>Ground. Notably, there was no significant correlation between surface roughness and flexural strength. Therefore, chairside polishing is a viable option for restoring the surface smoothness of zirconia restorations. However, for a more substantial improvement in flexural strength, reglazing is preferable to polishing.
*:statistically significant (p<0.05)*:statistically significant (p<0.05)